A New Benchmark
In Tableware Production
Schlemmer Prozess Systeme uses compact Simotion motion controllers in the modular design of rotary glassblowing machines. This results in reduced downtime, higher productivity, and optimized maintenance.
The idea of constructing modular rotary glass-blowing machines with 20 or more integrated — that is, individually exchangeable — stations or segments has been around for a long time. However, the technological capability to house all mechanical and, in particular, control and drive components in a minimal space was not available until now.
For an Asian glass manufacturer that required a new production line for flute glasses consisting of a 16-station stem press and a 24-station blow-molding machine, three companies from Germany and Austria developed a technologically and commercially convincing solution. In a very short time, Forma Glas GmbH from Neukirchen/Enknach, Austria; SPS Schlemmer Prozess Systeme GmbH from Deggendorf Germany; and Faschang Werkzeugbau GmbH from Weng im Innkreis, Austria, together developed the first modular rotary glassblowing machine in the world. Software development was supported by R&D funds from the Central Innovation Program for Small and Medium-Sized Enterprises (Zentrales Innovationsprogramm Mittelstand, or ZIM).
Achieving goals quickly with state-of-the-art automation technology
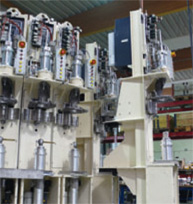
”The greatest challenge," said Heribert Schlemmer, managing director of SPS GmbH, "was to accommodate all control and drive components for the rotary motion of the blowing and servo lift station and for the lifting motion of the servo lift station in one cabinet in the segment. If a fault occurs that cannot be rectified immediately, the affected segment can be quickly removed from the process and replaced by an operational segment." That way, downtimes and waste product could be minimized and the required output of up to 40 cuts per minute (depending on the articles produced) could be achieved.
The new Simotion D410 PN for single-axis applications offered a powerful, modular, and compact motion controller for precise, sensitive servo control of the lifting motion of the servo lift station and setting the blowing pressure. When attached to a PM340 power module on the Sinamics S120 drive system, the device requires only minimal installation space, allowing sufficient room for two Micromaster converters, terminal modules, voltage supply, and peripherals in the switching cabinet.
Higher availability through optimized maintenance
This approach enabled a segment design that greatly facilitates maintenance. Thanks to quick couplings for air, water, and lubrication along with plug-in connectors for the power supply and communication at the distributed switching cabinets, trained production workers can replace a segment in less than five minutes. Replacing individual components is also easier because all the components of the drive lineup communicate via the digital Drive-CLiQ system bus and all settings are stored on a Compact-Flash card. An additional advantage is that the virtually standardized segments can be exchanged between multiple blowing machines, and to a certain extent also between machines with a higher or lower number of stations. Even the tower no longer features any components that cannot be replaced within a few minutes. This is a further improvement in terms of maintainability compared with machines that have a centralized design. Annual production has increased by at least 5 percent thanks to the new modular machine generation, says Rudolf Bernroitner, managing director of Forma Glas GmbH.
Fast networking via Profinet

The Profinet variant of the Simotion D410 is equipped with two Profinet ports via which all 2-4 stations communicate in real time (Profinet RT) with a Simotion D445-1 that works as a master. This high-performance motion controller is installed in the tower switching cabinet and linked to an additional Simotion D445-1 in the main switching cabinet located on the ground by slip ring connections via clock-synchronous Profibus and Industrial Ethernet. These two controllers are used to distribute formulations and target data to the individual stations and, conversely, for exchanging and centrally as visualizing current data and process information. In addition, the controller installed on the ground coordinates the servodrives and thus the interaction between the table drive, feeder machine, extraction, transfer, prepress, converter, and stem infeed.
As a certified Siemens Solution Partner for motion control solutions, SPS GmbH has been familiar with and used the Simotion system for more than four years. Here too, programmer Andreas Lindhuber incorporated all the available functions to synchronize the above-mentioned system components and to realize a fast and harmonious yet flexibly modifiable process. Furthermore, he exploited the integrated programmable logic controller (PLC) functions in the Simotion family and implemented process control in the motion controller. This has resulted in a superimposed PLC and, consequently, in a reduction in costs.
Moreover, the solution uses automatic recording and setting of the mold height for each station, which enables reworked molds to be used without manual adjustment and minimizes the waste quota. The machine design also allows using a dual transfer and servo press station so that significantly higher cut numbers can be handled if the products permit it. ”The high performance density in modern controllers will in the future enable us to fulfill specific customer requirements even more easily and cost-effectively," predicts Bernroitner, "either by integrating additional components or simply through a customized design of the user interface."
Straight forward user guidance
The second focus of enhancing the machine by means of a modular design was on even greater ease of use in terms of user guidance and improved process transparency. A prerequisite for this was the transfer of large data volumes via fast bus systems. A multilingual user interface was developed under Simatic WinCC flexible, which easily guides the user through the entire process. The operator can store optimized setting parameters for a certain product as a formulation on a one-off basis and document all required ancillary components in the formulation as well. This not only considerably reduces the setup time for repeating runs, but also allows operating stations with up to five different formulation sets. Another state-of-the-art feature is the remote access via a virtual private network tunnel if the maintenance staff requires support or if updates need to be loaded. This saves time and cost-intensive on-site service calls and frees automation staff capacity to perform other tasks.
Modularity brings benefits in all areas
Last but not least, the modular design is beneficial for dispatch and commissioning: the basic structure of the machine can be packaged and shipped separately from the blowing stations, resulting in reduced costs. Commissioning time can also be significantly reduced. The first modular machine was completely assembled at Faschang, measured by laser, tested in a dry run, and accepted by the operator. Only the segments need to be mounted on-site, connected, and briefly checked again. In fact, everyone involved prior to the first commissioning at the end customer’s facility is convinced that the new, modular machine generation will meet the high customer requirements and establish itself on the world market after its debut in Asia.