Erweiterung des Prozessleitsystems für die Wanne 2 bei HEINZ-GLAS
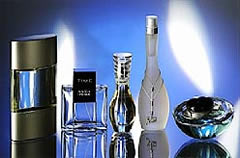
Schon 1998 entschloss sich die Firma HEINZ-GLAS ein durchgängiges Prozessleitsystem für Ihre gesamte Fabrik einzusetzen. Der Grundgedanke war, Schritt für Schritt bei Umbauten, Erweiterungen und Neubauten die gleiche Technik einzusetzen, um in der gesamten Fabrik auf die einzelnen Anlagenteile zugreifen zu können. Dazu war es nötig, ein System zu wählen, das über viele Jahre gepflegt und weiterentwickelt werden kann. Aus dieser Überlegung heraus hat sich die Firma HEINZ-GLAS für ein SIMATIC PCS7 System entschieden.
Im Januar 2001 wurde das vorhandene System, über das bis dahin nur die Gemengeanlage lief, um die neu gebaute Wanne 2 erweitert. Für die Realisierung dieser Erweiterung wählte HEINZ-GLAS die Firma Schlemmer Prozess Systeme GmbH als unabhängigen und kompetenten Spezialisten für Messtechnik, Regeltechnik und Prozessleitsysteme.
Schon bei den ersten Gesprächen stellte sich heraus, dass die Performance der eingesetzten Bussysteme nicht für den geplanten Endausbau der durchgängigen PCS7 Produktionsstätte ausreicht. Als Lösung wurde der PC-BUS von 10 MBit auf 100 MBit angehoben, und der AS-BUS vom 1,5 MBit Profibus FMS auf den Industrial fast Ethernet mit ebenfalls 100 MBit umgestellt. Bereits bei der Inbetriebnahme der redundanten Server PCS7-V5 sowie der Clients überzeugte diese Lösung durch die gewonnene Performance.
Um keine Daten von der Gemengeanlage während der Inbetriebnahmezeit zu verlieren, wurde ein alter Server mit der Version 4 vorübergehend als „Notbedienebene“ genutzt. Bei der Umstellung auf die Version 5.1 wurde diese Station dann als Client installiert, und dafür die Prozessbedienung am Server 2 eingestellt. Die Engineering Station wurde während der Inbetriebnahmen am Ort des „Geschehens“ (in der Schaltwarte direkt neben der Wanne) aufgestellt. Im Normalfall befindet Sie sich in der E-Werkstatt zur Systempflege und zum schnellen Beheben von Störungen.
Das Übersichtsbild Wanne 2 gibt einen schnellen Überblick über die regenerativ beheizte 65t Wanne mit Elektrozusatzheizung, die von der Firma Glashüttentechnik Grob GmbH & Co.KG gebaut wurde. Die Schmelzwanne wird momentan mit nur drei Feedern betrieben, der andere Feeder wird erst zu einem späteren Zeitpunkt in Betrieb genommen. Derzeit sind die Feeder 2, 3 und 4 in Funktion.
Da es sich um eine regenerativ betriebene U-Flammen Schmelzwanne handelt, wird ständig das Feuer abwechselnd links bzw. rechts eingeschaltet. Um eine gleichmäßig hohe Luftvorwärmung auf beiden Seiten zu erreichen wird nicht wie früher nur nach einem Zeitintervall gewechselt, sondern es fliesen mehrere Faktoren in die Wechselsteuerung mit ein. Den Wechsel selber steuert dabei ebenfalls die AS416 PCS7 Station, lediglich die sicherheitssrelevanten Teile (die Gasventile) werden hardwaremäßig angesteuert.
Sämtliche Detailbilder informieren schnell über den aktuellen Prozess, wie hier auf dem Bild Feeder zu sehen ist. Für die eingesetzten Regler hat die Firma SPS eigene Tools geschrieben, um die nötigen Genauigkeiten zu erreichen. Die wichtigsten Parameter (Sollwert, Istwert, Arbeitssollwert, Stellwert) werden schon im Übersichtsbild dargestellt. Im Regelkreisbild sind dann die Sonder-funktionen wie Kaskadierung, Thermoelementumschaltung usw. leicht bedienbar, wobei die Autorisierung für diesen Teilbereich Vorraussetzung ist.
Am Beispiel Trafo 2 ist die Bedienung dieser Anlagenteile ebenfalls übersichtlich möglich. Das lebenswichtige Kühlsystem sowie die Raumlüfter und alle Details, die zum Trafo gehören, sind vorhanden und bedienbar. Selbst die Leistungsregelung der Trafos ist in diesen Bildern bedienbar.
Der entscheidende Vorteil, der für den Einsatz von PCS7 in der Prozessautomatisierung spricht, ist der stets gegebene Gesamtüberblick über den Prozeß. Egal in welchen Teilbereichen sich der Anwender befindet, er verliert nie den Überblick über die Gesamtanlage. Eine neue Meldung erscheint immer oben in der Meldezeile, und außerdem wird die entsprechende Sammelanzeige aktiviert und zeigt die neue Meldung mittels Blinksignal an. Wird die Störung quittiert, so wechselt das Blinksignal in ein Dauersignal. Unterschieden wird dabei zwischen:
A = Alarm (low- oder high-alarm)
W= Warnung (z. B. Toleranz)
! = Einzelsteuerung bzw. Handbedienung
S = OS Leittechnik Meldung