Modernisierung einer Gemengeanlage bei Schott in Grünenplan
Das Prozessleitsystem SIMATIC PCS7 von Siemens dient als Basis des "Batch Control Systems"
Vor der Modernisierung erfolgte die Prozessführung des Gemengetransports sowie der Waagen mit 5 Bedienstationen mit einem PMS System von Philips sowie mit zwei Maschinenterminals von Siemens. Basis der Modernisierung sollte das Bedienkonzept der vorhandenen Anlage sein und es sollten die Erfahrungen des Anlagenpersonals berücksichtigt werden.
Das "Batch Control System" von SPS wurde mit folgenden Komponenten realisiert:
- OEE Kennzahlen
- Erstellung von Produktionsplänen
- Herstellungsnachweis
- Stammdatenlisten und Zeiterfassung
- Gemengelaufkarte
- Chargenreport
- Materialwirtschaft
- E-Mail Benachrichtigung
- Reinigungs- und Wartungsarbeiten Management
- freie Konfiguration (Laufwerkspfade, automatischer Protokolle, Störungskategorisierung)
- Datenaustausch (Excel, SAP) an einem Novell Server
Da es sich um eine komplette Erneuerung des Systems handelt musste für die Inbetriebnahme ein Konzept entwickelt werden dass die parallele Verwendung der bestehenden Hardware – Silos, Waagen, Gemengetransport und Mischer – sowohl für das bestehende PMS wie auch für das neue System zulässt. Die Gemengeproduktion konnte zu keinem Zeitpunkt länger als 8h pro Tag unterbrochen werden. Aufgrund des Umfangs wurde für die Inbetriebnahme insgesamt ein Zeitaufwand von bis zu 4 Wochen einkalkuliert. Dementsprechend wurde vor Inbetriebnahmebeginn sehr viel Zeit in die Entwicklung eines Konzepts, das die parallele Verwendung der Hardware für beide Anlagen zulässt, investiert.
Zur Bedienung und Beobachtung der Aggregate (Messstellen, Motore, Ventile etc.) wurden darüber hinaus sog. "Faceplates" eingesetzt. Es handelt sich dabei um zu einem Bedienobjekt vereinte Detailbilder, welche mit dem SPS-Programm verbunden sind und durch einen Mausklick aus dem Prozessbild heraus geöffnet werden können. Für jedes einzelne Aggregat ergeben sich daraus zusätzliche Bedien- und Beobachtungs-möglichkeiten - Klartextanzeige aller Störungen & Bedienmeldungen, Alarmeinstellungen, Betriebsarten-wahl, Zustandsanzeigen, Parametereingaben, Vorgabe von Wartungsintervallen, Wartungstexte etc..
Das Batch Control System
Als Basis zur Bedienung und Beobachtung fungiert das Prozessleitsystem PCS7. Auf dem PC werden prozessrelevante Anlagenzustände, Störmeldungen sowie Wartungsintervallmeldungen (Aggregate) angezeigt. Hierbei wurden bei der Fa. Schott AG Bildbausteine wie z.B. Waagen, Motore, Ventile usw. aus der PCS7 Library eingesetzt. Die Chargenerfassung, Chargenprotokollierung und -auswertung findet in einer SQL Datenbank (SQL Server 2000) statt. Die Weiterverwertung von Chargendaten erfolgt über das angebundene System SAP/R3, das zusätzlich angelieferte Rohstoffmengen an die Datenbank des Wiegesystems leitet. Zur Gewährleistung einer hohen Verfügbarkeit ist die Software für redundanten Betrieb ausgelegt - d.h. bei Ausfall eines Datenservers versorgt ein zweiter Server die Bedienstationen unmittelbar. Sämtliche Daten werden durch Verwendung der „Replikation“ des SQL Servers laufend synchronisiert. Auf sämtliche Daten kann ohne Durchführung eines „RESTORE“ über einen Zeitraum von bis zu 10 Jahren zugegriffen werden. Unter Verwendung der RESTORE Funktionalität gibt es keine zeitliche Beschränkung der Datenhaltung. Das auf der Basis von PCS7 arbeitende „Batch Control System“ der Fa. Schlemmer beinhaltet neben zahlreichen anderen Features unter anderem folgendes:
Die zeitliche Dauer einzelner Produktionsabläufe wird mit Chargennummer und Gemengesatznummer zu Recherchezwecken in einer Datenbank gespeichert. In Absprache mit Fa. Schott AG wurden für die vorliegende Anlage insgesamt 19 solcher „OEE“ Kennzahlen - zu jeder Charge – erfasst. In weiteren Schritten werden diese Daten zur Optimierung von Produktionsabläufen verwendet.
- Erstellung von Produktionsplänen
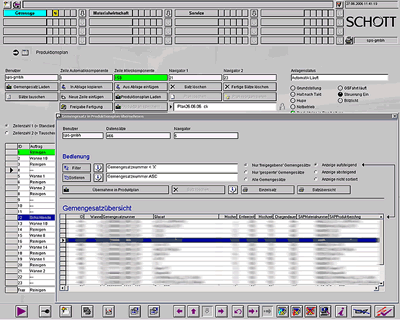
Die im Labor berechneten Gemengesätze werden in Form von Rezepten für die Erstellung des Produktionsplans bereitgestellt. Der Bediener wählt aus einer Liste von freigegebenen Rezepten den zu produzierenden Satz aus und trägt diesen an der gewünschten zeitlichen Abfolge im Plan ein. In diesem Plan kann die Produktion für einen Zeitraum von bis zu 1 Woche im voraus festgelegt werden. Der Produktionsplan beinhaltet zu jedem Gemengesatz zusätzliche Informationen wie Auftragskennzeichen, Ziel der Charge (Mischer, Reinigung etc.), Sollchargenzahl, Istchargenzahl, Status der Bearbeitung, Freigabe, Sollzeit der Bearbeitung, Istzeit der Bearbeitung etc.. Durch Verwendung des redundanten Serverpaares ist sichergestellt, das bei Ausfall eines Servers der zweite Rechner die letzte Version des jeweiligen Rezeptes bzw. des Produktionsplans zur Verfügung stellen kann. Im Labor wird entschieden welche Gemengesätze zur Produktion freigegeben sind bzw. welche Gemengesätze nicht freigegeben sind. Wird während der Produktion ein "gesperrter" Gemengesatz erkannt, so wird in den vorhandenen Rezepten automatisch nach der höchsten - für diese Glasart - vorhandenen Versionsnummer gesucht und diese zur Produktion herangezogen. Features zur Bearbeitung wie etwa die Verwendung einer Zwischenablage, das Laden bzw. Speichern von Produktionsplänen, das Tauschen, Löschen, Einfügen und freie Editieren von Gemengesätzen gehören dabei zu diesem „Batch Control System“ ebenso wie der Austausch von Produktionsplänen nach Excel. Sämtliche Menüfunktionen und deren Anwahl sind grundsätzlich einfach gehalten und annähernd über einen einzigen Mausklick zu erreichen.
Zu jeder Schicht - freie Vorgabe des Produktionszeitraums ist möglich - wird wahlweise manuell oder automatisch ein Herstellungsnachweis ausgedruckt. Der Herstellungsnachweis beinhaltet sämtliche zusammenfassende Angaben über die gefertigten Chargen. Die Auflistung erfolgt getrennt nach Wanne wobei zusätzliche Angaben zum zugehörigen Mischer, der mittleren Produktionszeit, der Glasart sowie der zu dieser Wanne gefertigten Chargennummern im Nachweis enthalten sind. Zusätzlich werden die während der Produktion aufgetretenen Störungen oder durchgeführten Wartungen an der Anlage aufgeführt.
- Stammdatenlisten und Zeiterfassung
Verwaltung von Anlagenpersonal mit ID, Nummer, Name etc. und sonstige benötigte Daten. Für die Erstellung des zur Schicht zugehörigen Herstellungsnachweises werden die Anlagenbediener aus den Stammdaten wahlweise über deren Personalnummer oder den Namen ausgewählt. Jede Schicht wird mit Angaben zu Beginn und Ende sowie dem Namen des zugehörigen Schichtführers protokolliert. Per Mausklick kann der Personalstamm in ein Excel Arbeitsblatt exportiert werden.
Zur Rückverfolgung des Gemenges wird für jede Charge wahlweise automatisch oder manuell eine kennzeichnende Laufkarte ausgedruckt. Diese Karte beinhaltet unter anderem Informationen zu Farbnummer, Wanne, Glasart, Schichtführer, Schicht, Glasgewicht etc. Zur leichteren Verfolgung der Chargendaten über Scanner beinhaltet diese Laufkarte die Chargennummer zusätzlich als aufgedruckten Barcode.
Zu jeder Charge wird wahlweise manuell oder automatisch nach einer Toleranzverletzung ein Ausdruck erzeugt. Der Report beinhaltet neben dem Bearbeiter und der Bearbeitungszeit je nach Glasart bis zu 470 kennzeichnende Werte zu dieser Charge. Das nachträgliche Anfertigen von Chargenprotokollen ist über einen Zeitraum von bis zu 10 Jahren möglich.
Anhand der gefertigten Chargen sowie der von SAP zur Verfügung gestellten Daten über Materialzugänge kann eine beliebige Recherche zur Materialbewegung durchgeführt werden. Durch Vorgabe von Start- bzw. Endzeitpunkt, Material, Glasart und Wanne werden unter anderem der Zu- bzw. Abgang des Materials, der wannenbezogene Rohstoffverbrauch, Toleranzwerte von Einzelkomponenten etc. dargestellt. Wie bei allen Funktionen zur Recherche ist auch in punkto Materialwirtschaft die Bedienung grundsätzlich sehr einfach gehalten, sodass der Bediener die notwendigen Informationen mit nur wenigen Einstellungen erhält. Alle Ergebnisse einer Recherche können nach Excel exportiert werden.
Unregelmäßigkeiten der Anlage werden per E-Mail an einen bestimmten Benutzerkreis gemeldet. Neben der E-Mail Adresse und dem Namen des Empfängers lassen sich unter anderem auch der Betreff der Mail sowie der Nachrichtentext in einem Menü frei konfigurieren. Dringlicher Wunsch der Fa. Schott AG war unter anderem das Melden von Fehlern die den Datenaustausch der Gemengeanlage von und zu SAP betreffen. Neben der E-Mail Benachrichtigung besteht in dem "Batch Control System" der Fa. Schlemmer optional auch die Möglichkeit der Benachrichtigung per SMS oder FAX.
- Reinigungs- und Wartungsarbeiten Management
Alle an der Anlage durchgeführten Reinigungs- und Wartungsarbeiten werden mit Beginn, Ende, Art sowie einem beschreibenden Text protokolliert. Anfallende oder überfällige Wartungsarbeiten können so anhand der automatisch erstellten Listen schnell lokalisiert werden. Ein Ausdruck kann wahlweise manuell oder automatisch mit Beendigung der letzten Schicht gedruckt werden. Per Mausklick ist es möglich den Report nach Excel zu exportieren.
Sämtliche notwendigen Einstellungen wie Laufwerkspfade, der automatische Ausdruck von Protokollen etc. sind wie allgemein für das „Batch Control System“ der Fa. Schlemmer üblich mit entsprechender Berechtigung frei konfigurierbar. Zusätzlich ist in dem System eine sog. Kategorisierung von Störungen integriert. D. h. die Anlage wird in Produktionszentren gegliedert für die im Störfall der Beginn der Störung, das Ende der Störung sowie die Stillstandszeit mit einem vom Bediener frei vorgebbaren Meldetext protokolliert werden. In einer folgenden Recherche (Anlagenoptimierung) können Schwachpunkte im Produktionsverlauf somit sehr schnell aufgedeckt werden.
Für den Austausch von Daten (Excel, SAP) wurde das „Batch Control System“ an einen NOVELL Server angebunden. Besonderer Wunsch der Fa. Schott in Grünenplan war es einen kompletten Betrieb auch ohne Anlagen PCs zu ermöglichen. Hierfür wurde ein Konzept entwickelt welches das Einbringen der umfangreichen Rezepte - bis zu 470 Einzelwerte - in die SPS Steuerung auch ohne das Vorhandensein eines an das „Batch Control System“ angebundenen Rechners erlaubt. Als Basis dieses Konzepts werden die Gemengesätze durch einen beliebigen anderen nicht zur Anlage gehörenden PC auf eine "CF" Karte geschrieben. Über ein per Profibus an die Steuerung angebundenes Text Panel werden folgend die Rezepte von diesem Datenträger eingelesen. Sämtliche Handfunktionen, das Steuern der Wiegeabläufe sowie eine Störauswertung mit Recherchemöglichkeit sind für den Notbetrieb ebenfalls in diesem Panel integriert.
Waagen und Dosiersteuerung
Als grundlegende Programmiersprache kommt in PCS7 Systemen der sog. "Continuous Function Chart" (CFC) zum Einsatz. Vorhandene Funktionen werden graphisch verknüpft und führen auch ohne tiefe Programmierkenntnisse schnell zu einem Ergebnis. Die Programmierung der Abläufe erfolgte bei der Fa. Schott im sog. "Sequential Function Chart" (SFC) des PCS7 Systems. Dieses grafische Programmiertool erlaubt es, den Ablauf anhand von Schritten (Blöcken) und Transitionen (Weiterschaltbedingungen) zu formulieren. Im "Runtime" System (Visualisierung) wird ein solcher "SFC" durch einen Mausklick geöffnet, der aktuelle Zustand des Ablaufs wird farblich dargestellt - die Zuordnung der Farben zu den jeweiligen Zuständen ist frei projektierbar. Fehlerquellen die zu Produktionsausfällen führen, können mit diesem Hilfsmittel auch ohne Programmiergerät sehr schnell diagnostiziert und behoben werden.
Die zu verwiegenden Rohstoffe sind über einen, dem Silo zugeordneten, Konfigurationsdialog parametrierbar. Jeder Rohstoff erhält für den Dosiervorgang zusätzlich einen Satz an Daten - Feingewicht, Nachlaufgewicht, Tippzeit, Dosierart, Waagenzuordnung, SAP Nummer etc.. Der Wert für die Abschaltung des Feinstroms kann, sofern angewählt, von der Hardware automatisch optimiert werden. Im Statusbild der laufenden Dosierung werden getrennt für jede Waage die zu verwiegenden Rohstoffe mit dem aktuellen Zustand bzw. dem Verlauf der Verwiegung dargestellt.
Je nach Wertigkeit der Dosierabfolge werden die Rohstoffe in unterschiedlicher zeitlicher Reihenfolge in den Waagenbehälter dosiert. D.h. ein Rohstoff mit höherer Wertigkeit wird vor einer Komponente mit niedrigerer Wertigkeit dosiert. Dieser Wert steuert auch die zeitliche Abfolge für das Entleeren der Rohstoffe aus der Waage. Je nach Wertigkeit der Dosierabfolge wird eine Waage vor einer anderen entleert.
Mit der Umstellung der Wiege- und Dosiertechnik auf das "Batch Control System" aus dem Hause SPS Schlemmer Prozess Systeme GmbH hat sich die Fa. Schott AG zukünftig alle Optionen in Punkto Erweiterbarkeit, Wartung und Kostenminimierung eingeräumt. Die Abhängigkeit von nur einem Lieferanten gehört damit der Vergangenheit an. Als kompetenter Partner unterstützt die Fa. Schlemmer Prozess Systeme GmbH Kunden im In- und Ausland bei der Realisierung von Projekten.